
This paper discusses the methods, advantages, and limitations of finite element
analysis for the design of ultrasonic resonators (resonators/sonotrodes/probes, boosters,
and transducers/converters) for power ultrasonics. Typical examples are given.
This paper was originally presented at the Ultrasonic
Industry Association's 1991 technical symposium, when it was titled "The
Application of Finite Element Analysis to the Design of Ultrasonic Resonators".
It has been updated to reflect current practices.

Finite element analysis (FEA) is a computer-based method for analyzing and improving
resonator performance. (Note: FEA is sometimes called FEM -- finite element method.) In
FEA, the resonator is simulated as a computer model. The computer simulation model
consists of a large number of small "elements" that represent (approximately)
the shape of the resonator. Each element can be described mathematically by a set of
equations. The solution to this set of equations yields a prediction of the
resonator's performance -- i.e., the natural frequencies at which the resonator will
vibrate and the amplitudes and stresses associated with each of these frequencies.
After the performance has been predicted, the resonator's dimensions or materials can be
changed within the FEA model in order to improve the performance.
The following discussion will emphasize FEA of medical probes, as used phaco
emulsification (cataract surgery) and similar applications. However, FEA is equally
applicable to the design of industrial resonators. For examples, including animations, see
bar horns, block horns, cylindrical horns, and boosters.
Notes:
- The resonators discussed below have a nominal axial resonance of 25 kHz, although any
design frequency is possible.
- See the glossary for definitions and symbols.

In order for a resonator to function properly, consideration must be given to the
following performance factors.
- Primary resonance tuning. The frequency of the primary
(desired) resonance must be adjusted to the nominal resonance of the power supply
(generator). This frequency must account for the expected operating temperature of the
resonant stack.
- Secondary resonance tuning. The resonator must have
sufficient frequency separation between the primary and all secondary (undesired)
resonances. Otherwise, the power supply may accidentally "jump" to a secondary
resonance, especially during the transient starting conditions or under highly loaded
conditions. Such a jump could cause poor or erratic performance and could overstress the
resonator. Poor frequency separation may also cause nonuniform or asymmetric resonator
amplitudes, which may lead to early transducer failure.
- Gain. The resonator must have sufficient gain (output
amplitude) to perform the application.
- Amplitude uniformity. The amplitude at the resonator's face
must be sufficiently uniform to perform the application. The amplitude at the resonator's
input surface must be sufficiently uniform to prevent heating and galling at the joint
interface. (These requirements apply mainly to industrial horns, whose face and
input surfaces may be relatively large and are therefore prone to significant amplitude
variations over these surfaces.)
- Amplitude direction. The predominate amplitude should be in
the desired direction in order to maximize the effectiveness of the ultrasonics while
minimizing undesired side effects (heating, scrubbing, wasted power, etc.). The desired
direction is generally along the axis of the resonator, although there are notable
exceptions -- e.g., radial resonators (disks and tubes) or flexural resonators (plates,
strips, disks, tubes, dental prophylaxis probes, etc.).
- Node location. If the resonator is to be mounted at a node,
then the mounting flange must be properly positioned at the node so that minimum energy is
transmitted to the support structure.
- Stress. The stresses must be sufficiently low for long
resonator life.
- Loss. The loss must be low to avoid associated problems
(thermal runaway in piezoelectric ceramics, tissue heating, operator discomfort in
handheld devices, etc.).
- Starting. The resonator must achieve the operating
amplitude within the time permitted by the power supply. Thus, the energy distribution
within the resonator and between the resonator and booster must be considered.
In addition to these performance considerations, the following must also be considered.
- Materials. Materials must give adequate fatigue and
wear/erosion life. For medical probes, the materials that are in contact with tissue
must not cause detrimental effects; also, the materials and design must be amienable to
sterilization, if required.
- Geometry constraints. The resonator must fit within a
geometry envelope. For a handheld medical probe, the probe must be lightweight and
relatively slender. For plastic welding horns, the horn must conform to the shape
of the part.
- Maunfacturability. The resonator must be
manufacturable at reasonable cost.

First, consider the conventional approach to resonator design.
- Design the resonator. The resonator's design is based on
the engineer's experience and best judgement.
- Machine and tune the resonator to the desired frequency.
Care must be taken not to mistune or tune to a nonprimary resonance.
- Evaluate the resonator performance. Determine if the
resonator meets the performance requirements.
- Correct the known problems. If the resonator's performance
is not acceptable, then modify the existing resonator and repeat step 3 or, if required,
start again from step 1.
- Ship the resonator. Wait for the customer to find
additional problems (usually fatigue failure) associated with extended use.
- Correct the customer's problems. Start over from step 1.
There are at least two problems with this approach.
- This cut-and-try approach wastes time and material. The
resonator performance parameters cannot be determined until a prototype resonator has been
machined. If the prototype resonator does not have adequate performance or if it cannot be
remachined to achieve adequate performance, then additional resonators may be required.
This rework creates scheduling difficulties and delays delivery.
- Resonator reliability will be difficult to estimate. This
is because certain performance parameters cannot be easily evaluated. For example, there
is usually no convenient way to determine resonator stresses, so estimates of resonator
life will be crude. (Note: even if holographic or thermographic equipment is used for
stress measurement, this equipment will only show surface stresses, not the internal
stresses which may be most critical.) Similarly, amplitudes at the joints (e.g., between
the resonator and booster) will be impossible to measure, so joint problems will be
difficult to detect. Thus, evaluation of resonator reliability is often left to the
customer.

Unlike conventional resonator design, FEA attempts to solve the performance problems before
the resonator is machined. The process has eight steps.
- Specify the
performance factors
- Establish the
material properties
- Model the resonator
- Process the model
- Evaluate
- Iterate
- Machine and tune the
resonator
- Verify the performance
These steps may be applied to a conceptual resonator whose performance is unknown or to
an existing resonator whose performance is inadequate.
The following steps will be illustrated with a medical probe (figure 1) whose primary
axial resonance is at 25 kHz. The probe is driven by a power supply (generator) which
delivers electrical energy to the piezoelectric ceramics. This causes the ceramics
(and, hence, the probe) to expand and contract at the probe's resonant frequency.
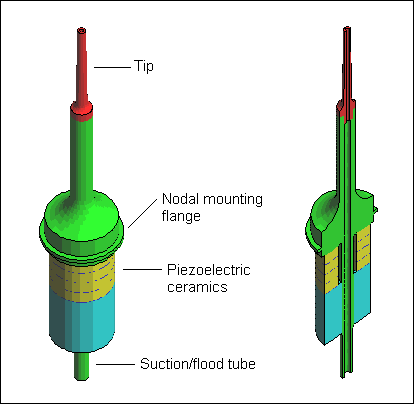
Figure 1. Typical medical probe.
Left: full model
Right: sectioned model
The engineer must first decide what performance factors are important for the
particular resonator. This will dictate certain requirements for the computer model, which
will determine the time needed to complete the FEA. See Requirements
for Adequate Resonator Design.
(Specifics are discussed in the section Modeling Considerations.)
The engineer must establish the material properties that will be used for subsequent
FEA. These properties can be determined from ultrasonic tests or static tests, or, less
preferably, can be estimated from handbook values.
Alternately, the engineer can run a preliminary FEA (as described in the following
sections) on an existing resonator that has the same material and similar dimensions to
the conceptual resonator. The material properties are then adjusted until FEA adequately
predicts the measured performance of the existing resonator.
During the modeling phase, the engineer constructs an idealized computer model of the
actual resonator. The model is composed of a large number of small elements that are
sufficient to describe the geometry of the resonator. This is called "creating the
mesh". The mesh intersections are called nodes. The mesh elements must be
sufficiently small that the solution for the desired results will converge. (See section
on Modeling Considerations.)
The previously determined material properties are also specified.
In the following figure, only half of the resonator has been modeled because of axial
symmetry. By reducing the number of elements, the analysis time is significantly reduced.
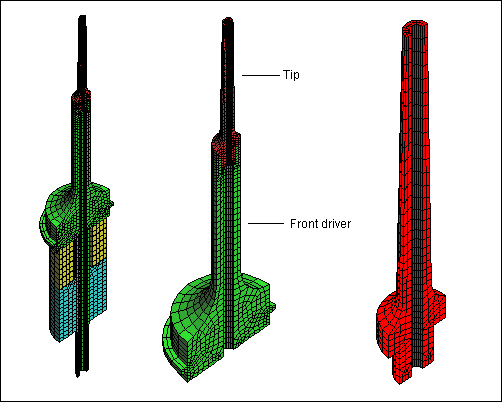
Figure 2. Resonator model (1/2 section) with element mesh (black lines)
Left: Complete resonator
Middle: Enlarged view of tip and front driver
Right: Enlarged view of tip
Depending on the model, the engineer may also have to apply certain boundary conditions
so that the model will not vibrate in unrealistic directions.
Most FEA programs have CAD-like preprocessors that aid in constructing the model and
the mesh.
Once the model has been completed and verified, it is submitted for processing.
The computer solves the required equations and outputs the results.
When the processing is complete, the engineer must check the output to determine if the
predicted resonator performance is acceptable (e.g., uniformities, stresses, frequency
separation, etc.). The following figures show typical results.
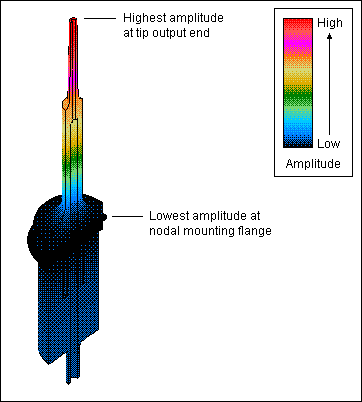
Figure 3. Axial mode at 25.0 kHz: relative amplitudes
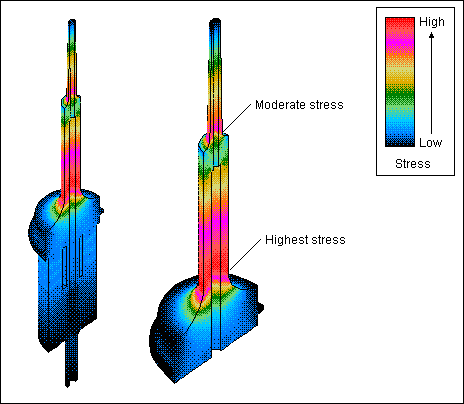
Figure 4. Axial mode at 25.0 kHz: relative stresses.
Left: Complete resonator
Right: Enlarged view of tip and front driver
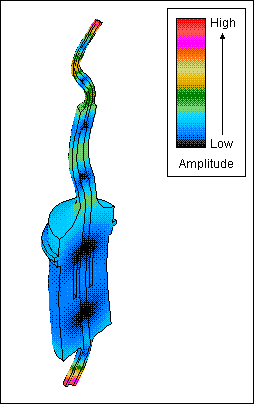
Figure 5. Bending mode at 23.8 kHz: relative amplitudes.
If the resonator performance is not acceptable, then the engineer must return to the
modeling phase and adjust the resonator dimensions. The revised model is then submitted
for processing. This process continues until adequate resonator performance has been
achieved, or until no further performance improvement seems possible.
After the performance of the FEA model has been correctly adjusted, a resonator is
machined to the dimensions of the FEA model. The resonator is then tuned to the specified
frequency.
If the FEA has been performed properly, then the performance predicted by FEA should
agree reasonably with the actual resonator performance. Agreement should be especially
good if similar resonators have been previously modeled. Exact agreement should not be
expected, either because of limitations of the FEA or because of measurement errors
for the actual resonator.
Frequencies
Frequencies are easiest and most accurate parameter to measure and verify. However,
note that FEA may predict more frequencies than can be measured in the actual resonator.
These extra FEA frequencies are often bending resonances or resonances where a node that
runs through the resonator's axis. Although such frequencies are actually present in the
resonator, they often cannot be easily excited by the transducer and are therefore
difficult to detect by frequency analyzer equipment. Although these extra resonances can
often be ignored, they can sometimes interact with the primary resonance, causing
asymmetric amplitudes and high stress.
In some cases, the extra FEA frequencies are caused by boundary conditions that are
needed to constrain the FEA model. Such FEA frequencies are erroneous and will not exist
in the actual resonator. It is the responsibility of the FEA engineer to recognize this
situation.
Amplitudes
Amplitudes are relatively easy to verify, but care must be taken to assure that the
amplitudes and their locations are correctly measured. This is especially important where
the amplitude changes rapidly (e.g., at the edge of large-diameter unshaped cylindrical
resonators). Depending on the sophistication of the amplitude measurement equipment and
the care of the operator, 5% amplitude difference between the measured values and the FEA
values would not be unusual.
If the FEA frequencies or amplitudes have larger error than expected, this may indicate
improper modeling (e.g., not enough of the resonator or improper boundary conditions),
inadequate mesh refinement, incorrect material properties, or incorrect measurements.
Stress
Since empirical stress data is usually not available, stress usually cannot be directly
verified. However, the FEA stresses will not be correct if the FEA amplitudes are not
correct, since stress depends on the amplitude gradient. Even if the FEA amplitudes are
correct, the FEA stress may still be incorrect due to poor choice of element sizes or
geometry. Some FEA programs permit estimates of FEA stress error and indicate where the
mesh needs to be refined to reduce the error.
The inability to verify FEA stresses may not be a problem, since the FEA engineer may
not be concerned with absolute stress values; he may only want to know if the stresses
have improved between successive FEA designs. This is especially true where the fatigue
properties of the resonator material are unknown, in which case the resonator life cannot
be predicted anyway. (See the section on Technical Limitations of FEA/
Predicting resonator Life.)

From the above discussion, the advantages of FEA are apparent. Compared to conventional
resonator design, FEA permits a substantially complete resonator design before any
machining begins. Because FEA gives information that is not available with conventional
resonator design, the resonator performance can be optimized to an extent that would not
otherwise be possible. FEA can indicate potential performance problems and, if these
cannot be corrected, subsequent reliability testing can focus on these problems.
The use of FEA must be balanced against the payback. The main constraint on FEA is the
time required to input the initial FEA model, where the modeling time grows exponentially
with the complexity of the resonator, and the time required to optimize the design. Thus,
FEA can best be used in the following situations.
If the customer has an application where resonator failure and replacement would be
costly (e.g., in an automated assembly line) or might result in injury (e.g., medical
probes), then the resonator must be designed for maximum life. FEA allows internal
resonator stresses to be analyzed and minimized before the resonator is machined. If the
"optimized" stress still appears too high, the application may be redesigned to
permit use with resonators of lower stress. If this is not possible, then the customer can
be informed of the risks, and the resonator can be given the appropriate warrantee.
Such high volume resonators (transducers, boosters, certain resonators) can be analyzed
to optimize the design. The resulting FEA cost per resonator is small.
Certain resonator modifications do not lend themselves to cut-and-try methods. For
example, if a resonator will use angled slots for improved uniformity, it would certainly
be more cost-effective to analyze different slot angles by FEA than by machining many
different resonators, each with a different slot angle. FEA can also provide information
on stresses, which would not be available through cut-and-try.
Even after machining, the actual resonator may not provide the information that is
needed to evaluate its performance.
With conventional resonator design, surface stresses can be measured after the
resonator has been made, although this requires sophisticated test equipment. In contrast,
FEA can predict both static and dynamic internal stresses before the resonator has been
made. For example, if any of the stresses in figure
4 had been excessive, then this resonator could have been redesigned to reduce these
stresses. If the fatigue characteristics of the material are known, then the resonator
life can be estimated.
FEA can predict ultrasonic amplitudes throughout the resonator. This can be useful for
determining node locations on boosters and transducers (figure 3). It can also be used to determine
the amplitudes at inaccessible location (e.g., the amplitudes across interfaces such as
horn-booster joints and ceramic interfaces). This can provide insight into problems such
as interface heating and galling.
In addition, FEA can predict amplitudes that cannot be easily measured. For example,
FEA can predict the transverse amplitudes on the face of a horn, which may cause scrubbing
problems or excessive transverse vibration of attached pins (as used for ultrasonic
machining of ceramics). Many measurement devices (e.g., lasers) cannot measure such
amplitudes.
FEA can predict asymmetric modes that cannot be readily detected by spectrum analyzers
(figure 5). As discussed above in the
section on verifying the performance, these modes can interact with the axial resonance,
causing asymmetric amplitudes and high stress in the axial mode. Early detection by FEA
allows these frequencies to be repositioned with respect the axial resonance, so that
their effects are reduced.
In certain circumstances, the variability of empirically measured data masks the
effects of design changes. For example, when machining a transducer to improve its
performance, the transducer must often be disassembled between each machining operation.
However, each disassembly-reassembly operation introduces additional variables
("noise") which can obscure the effect of the machining operations.
Variability of empirical data also occurs from variability of material properties. For
transducers, variability is caused by differing ceramic performance. In titanium,
variability may occur between batches of material.
FEA eliminates these kinds of variability problems. With FEA, the effects of any design
changes are exactly repeatable and all performance changes can be directly attributed to
design changes.

While FEA could conceivably be used to model almost any resonator, it will not be
practical or cost-effective in all situations. The following are general limitations which
may be overcome in specific instances.
Some of FEA's limitations arise from difficulties in creating an adequate model of the
resonator. This is especially true for resonators with complex geometries (e.g., heavily
contoured resonators or composite resonators) that require three-dimensional models.
As discussed in the section on Modeling Considerations, the
model is often simplified in order to reduce modeling and computing time. Such a model
will always give somewhat limited or incomplete results. The FEA engineer must have
sufficient experience to estimate the effect of such simplifications.
FEA can predict resonator stresses. However, resonator stresses do not allow life
predictions unless the fatigue characteristics of the resonator material are known.
Unfortunately, there are significant problems in determining fatigue characteristics.
Fatigue can be affected by the frequency of vibration, so that conventional (low
frequency) handbook data may not predict the fatigue at ultrasonic frequencies. Even where
it might be reliable, low frequency data is usually too limited to provide life
predictions at ultrasonic frequencies. For example, low frequency tests are often stopped
at 500 million cycles, which represent only seven hours of continuous ultrasonics at 20
kHz.
Further, fatigue is affected by the raw stock type (rod, bar, or plate), the raw stock
size, and the direction of vibration relative to the material's grain. For nominally
equivalent material, fatigue may also vary from heat-to-heat (especially for titanium) or
among different manufacturers.
Fatigue is also affected by machining, which can leave residual tensile stresses that
shorten resonator life. These stresses are difficult to predict, since they depend on such
factors as material removal rate, the type of machining coolant, the tool sharpness, etc.
FEA cannot predict these surface stresses.
Thus, unless the material's fatigue properties and the effects of machining are well
known, the stresses predicted by FEA probably cannot be used to predict resonator life.
However, the FEA stress data can be used to redesign resonators that have known failure
problems.
Note: although this is listed as a limitation of FEA, it is also a limitation of any
other method of resonator analysis. The resonator life cannot be predicted from stress
unless the material's fatigue characteristics are known.
In most cases, joints are simply modeled as if the joined components were welded
together. Although this approach works well in predicting most performance factors, it
does not allow prediction of joint problems arising from fretting or slippage.
Such joint problems can occur at the booster-resonator joint because of nonuniform
amplitude at the interface. Joint problems can also occur in the transducer because of
flexing resonators or because of inadequate ceramic clamp force. Other joint problems
occur at threads (e.g., for tips, studs, transducer stack bolt).
In order to model such joint problems, the joint friction must be known. However, this
friction may change with time as joint fretting progresses.
In some cases joint problems can be predicted based on amplitudes and uniformities at
the joint, but the extent of the problem can only be determined when the actual resonator
is tested.
Stack loss includes the material loss of the resonator, booster, and transducer, the
radiated air loss, and the frictional loss at the stack joints. If the FEA program
calculates the stored energy of the model, then the resonator and booster material loss
can be calculated if their material's Q's are known. (Q is a material property that
relates the energy stored to the energy dissipated per cycle.) The material loss of the
transducer is much more difficult to estimate (see below). Prediction of radiated air loss
may be possible by FEA. As previously discussed, FEA cannot reasonably predict frictional
loss, especially loss caused by flexure.
FEA can predict the performance of a resonator under load. However, the analysis may be
extremely difficult. This is because the load may have nonlinear characteristics and the
load's characteristics may change as the ultrasonic process progresses. This would be
true, for example, in plastic welding and metal welding. Because of these problems, the
effect of the load is generally ignored during resonator design.
Although a FEA frequency response analysis can give some insight, FEA cannot predict
power supply starting problems or the tendency of the power supply to jump to a nonprimary
resonance under heavy load.
FEA can predict bending modes. However, in order to do so, the entire resonator stack
must be modeled. For example, to analyze the bending modes for a plastic welding stack,
the horn-booster-transducer assembly would have to be modeled. Compared to modeling a
single component (typically the horn), this causes the following problems.
- The modeling time may be much longer. This is because extra
components (e.g., the booster and transducer) must be added to the model. In addition, the
complexity of the model may increase. For example, where an axisymmetric model might
normally be used, extraction of bending modes will require a 1/2 3-D model (minimum).
- The analysis time will be much longer. With the added
components, the size of the model (number of elements) increases. Also, the number of
extracted modes increases.
- Bending modes depend on the stack components. If a stack is
analyzed with a particular transducer-booster, then the bending modes will change if
another transducer or booster is substituted. Since horns are often required to run with
several different boosters or transducers, analysis of all possible combinations is
usually not practical.
Also, in those cases where the bending involves microslip of the transducer's ceramics
(a nonlinear phenomenon), the FEA predictions may not be accurate. Thus, unless bending
modes are suspected of causing problems, they are often ignored, especially in the initial
analysis.
Unless the FEA program contains an element type that describes the operating
characteristics of piezoelectric ceramic, it cannot predict the output amplitude of a
transducer due to a specified electrical input.
FEA can analyze heat transfer problems. However, FEA has limited ability to predict
transducer temperatures. This is because the heat generation within ceramics depends on
many factors (e.g., the drive voltage, the load, the ceramic age, the time since the
transducer was assembled, the static preload, the insulation used on the ceramics to
prevent arcing, variations among ceramics, microslippage at ceramic interfaces, etc.).
These factors make it difficult to accurately characterize transducer heating.
Despite these limitations, FEA is still useful in transducer design. FEA can predict
static preload stresses , resonant frequencies, the node location , the relative amplitude
distribution, and stresses relative to the output amplitude. See figures 3, 4, and 5.

If the purpose of the FEA is to analyze an existing resonator design, then this can
usually be done within several days. Obviously, the time required will depend on the
complexity of the resonator and the complexity (or degree of simplification) of the FEA
model.
However, if the purpose of the FEA is to improve (optimize) the performance of a
resonator, then the time required can be considerably longer. The time required will
depend on the complexity of the resonator and the model, the number of performance factors
that must be improved (e.g., uniformity, stress, gain, etc.), the degree of improvement
required, and the acoustic engineer's knowledge about how to resolve the resonator's
problems. The resonator design must be repeatedly altered and rerun until an acceptable
design has been achieved.
A difficult resonator may require a week or more to optimize (excluding the time needed
to actually make the prototype resonator and verify the FEA performance). Even with this
effort, the results may not meet the optimization goals. Sufficient time must be allocated
for this optimization process.

In order to properly compare FEA to conventional resonator design, the considerations
for developing the computer FEA model must be understood.
The FEA model is a computer approximation of an actual resonator. The error of this
approximation will depend on the refinement of the model. Although refined models give
better results, they require more engineering and computing time. The degree of refinement
will depend on two factors.
- Selection of performance factors. The engineer must decide
what resonator performance factors (frequencies, amplitudes, stresses) are important for a
particular resonator design. The engineer then constructs an FEA model which will
adequately predict the specified performance factors.
- Convergence requirements. The FEA results will converge to
a solution as the mesh is refined and as the mesh more closely approximates the actual
resonator geometry. (Note: convergence does not necessarily imply accuracy.)
Frequencies
The refinement of the FEA model will depend on which modeshapes are considered
important. Flexure (bending) modes depend on the dimensions of the entire stack (resonator
+ booster + transducer). Therefore, if flexure modes are important then the entire stack
must be modeled in three dimensions. Unless the stack is axisymmetric, the required model
may be very time consuming to develop.
Even if such a 3-D model was developed, it would have limited usefulness in predicting
flexure. First, flexure modes may involve slip of the transducer ceramics and will,
therefore, be amplitude dependent (nonlinear). This will preclude correct prediction of
flexure frequencies. Second, flexure modes depend on the specific stack components. If the
customer uses a different booster or transducer than was originally modeled, then the
model will not predict the customer's flexure resonances. Thus, flexure resonances (which
seldom cause problems in actual practice) are generally ignored during initial FEA.
If the flexure modes can be neglected, then reasonable frequency accuracy can usually
be achieved by modeling only the resonator (i.e., no transducer or booster). Further, if
the resonator is symmetric and certain asymmetric modes can be ignored, then further
simplifications of the model are possible. Cylindrical resonators which are symmetric
about their stud axis can often be modeled axisymmetrically (a two-dimensional
approximation).
While modeling only a section of the resonator will save modeling and computing time,
it also limits the FEA results, since asymmetric modes may not be extracted. For example,
a 20 kHz 100 mm diameter unshaped cylindrical resonator will have a asymmetric
"shear" resonance adjacent to the axial resonance, which will cause significant
amplitude asymmetry for the axial resonance. Neither an axisymmetric model nor a 1/2 3-D
model would predict the asymmetric resonance; only a full three-dimensional model could do
so. Of course, the three-dimensional model is more difficult to design and more
time-consuming to run.
All resonators will have flexure and asymmetric modes. A limited FEA model that
precludes these modes can lead to unexpected problems when the actual resonator is
machined. Unfortunately, the effect of these modes on resonator performance cannot usually
be predicted in advance. In some cases, however, experience with previous resonators can
provide some guidance.
Amplitudes
The sophistication of the FEA model will depend on which amplitudes need to be
predicted. For example, axisymmetric models predict amplitudes across the resonator
diameter, but not around the resonator's circumference. If circumferential amplitudes are
important, then a 3-D model is required.
Stress
If the engineer is confident that the resonator will not fail, then FEA does not have
to give accurate stress predictions. This can considerably simplify the FEA model.
For example, if stresses are unimportant, then slots can approximated as rectangles
with "square" ends, rather than rounded ends. This approximation will have
little effect on the resonant frequencies or amplitudes. However, such a model could not
possibly predict the stresses at the slot ends.
If the resonator stresses are important, then the slots would have to be modeled with
rounded ends, which could significantly increase the modeling time. This is because the
mesh at the rounded ends may need to be adjusted by hand, especially at slot
intersections. The computing time also increases because of the increased number of
elements needed to model the rounded slot.
FEA estimates the performance of the actual resonator. As the size of the FEA elements
is reduced (i.e., as the mesh is refined), each performance factor will converge to its
terminal value. The rate of convergence will depend on the particular performance factor
and on the skill used to refine the mesh. Note: convergence does not necessarily imply
accuracy.
Frequencies and amplitudes
Generally, the frequencies converge most quickly their final values; amplitudes
converge more slowly.
Stress
Stress, which depends on the gradient of the amplitude (i.e., the strain), may require
a much finer mesh, especially at stress concentrations (e.g., at radii, slot ends, etc.).
The required mesh size for stress convergence will depend on the geometry of the
particular stress concentrator. Some FEA programs provide estimates of stress error, which
indicates where the mesh must be refined to reduce the stress error. (These estimates of
stress error assume that the frequencies and amplitudes have essentially converged.)
Thus, consideration of performance and convergence will determine the complexity of the
model. As the complexity increases, both modeling time and computing time may increase
substantially. Thus, the model should be kept as simple as possible, consistent with the
desired results. As discussed above, however, the required degree of simplicity cannot
always be judged in advance.
The usual approach is to model the resonator in the simplest manner that the engineer
deems prudent. This requires good familiarity with both FEA and ultrasonic resonators. If
the FEA results do not adequately predict the frequencies or amplitudes of the machined
resonator, then a more sophisticated model will be needed.

FEA will not be useful unless it gives accurate results. As discussed previously, the
user must be sure that the FEA solution has converged. However, a converged solution does
not necessarily imply an accurate solution. Accuracy will depend on several factors.
FEA cannot correctly predict resonator performance unless the resonator's material
properties (Young's modulus, modulus of rigidity, Poisson's ratio, and density) are known.
For resonators with small lateral dimensions, the density and the modulus of elasticity
(which determine the thin-wire wave speed) determine the resonant frequencies. The axial
frequency of a 20 kHz resonator will change by 100 Hz for every 1% error in the modulus of
elasticity or density.
For larger resonators, the resonant frequencies are affected somewhat by Poisson's
ratio. Depending on the resonator's shape, the amplitude can also be significantly
affected by Poisson's ratio.
For materials that are reasonably isotropic (e.g., most aluminums), only two elastic
property values are needed to completely characterize the material. These properties are
relatively easy to determine. For materials such as titanium and piezoelectric ceramics
that are orthotropic (i.e, the properties depend on the test direction), nine elastic
property values are needed for complete characterization. However, using averaged material
values (i.e., assuming that titanium is isotropic) usually gives reasonable results. A
further problem with titanium is that its properties may vary from batch to batch and may
also depend on the size of the raw stock.
Where resonator frequencies are concerned, a small error in the material properties is
usually not critical, since most resonators allow some extra material for tuning. However,
fixed-length resonators (e.g., transducers and boosters) do not enjoy this allowance.
In general, then, some FEA error should be expected due to inexact material values.
The FEA model must accurately represent the actual acoustic system. This means that the
geometry must be correctly modeled and boundary conditions must be correctly enforced.
The model geometry should reasonably approximate the actual acoustic system. (See the
section Modeling Considerations
for further discussion of modeling fidelity.)
Sometimes a seemingly insignificant change in geometry can dramatically affect the FEA
predictions of resonator performance. For example, omitting a stud from a horn with large
lateral dimensions (e.g., block horns, spool horns, etc.) can significantly affect the
amplitudes and stresses, although the effect on resonant frequencies may be minor.
The transducer-booster components usually do not have a significant effect on the
primary mode. However, these components can significantly affect the frequencies predicted
for other modes. (See Predicting
bending modes.) Therefore, if the horn is modeled without the transducer-booster, then
the optimized FEA design must allow extra frequency separation between the primary and
nonprimary modes in order to compensate for this potential error.
Note: even in the primary mode, the transducer-booster may have an effect if the
interfaces are not properly designed. For example, this can occur when a
transducer-booster is attached to a flexing disk if the disk has significant bending
across the interface joint.
In order to determine the effects of adjacent resonances on the primary resonance, an
estimate of the damping (Q) at each natural frequency will be needed. However, such
damping estimates are imprecise, often because the damping characteristics of the
transducer may not be well known. This will introduce some error, especially when the
damping is high (low Q).
If the resonator has been properly modeled and the solution has converged and the
material property values are accurate, then FEA frequencies and amplitudes are usually
within several percent of the measured (empirical) values. FEA gain is usually within 5%
of measured values.
Remember, however, a measured value is not necessarily an accurate value. This is
especially true for gain measurements, which involve indirect measurement of the resonator
input amplitude. Thus, disagreement between empirical measurements and FEA values does not
necessarily mean that the FEA values are incorrect.

This paper has described the advantages and limitations of FEA as compared to
conventional resonator design. As with any tool, FEA is not appropriate for all occasions.
However, for those occasions that warrant its use, FEA can provide insight and design
opportunities that would otherwise be impossible.
If you have a resonator design that might be improved by finite element analysis, then
you can use the Resonator Information Form to submit
baseline information or you can contact Krell
Engineering directly.

3-D -- three-dimensional.
asymmetric resonance -- a resonance in which the
amplitudes are different at symmetric locations on the resonator.
asymmetry -- an aberrant condition
in which vibration motion at two or more geometrically identical locations (e.g., the four
corners of a block horn) are not identical (within measurement tolerance). This may occur
with resonators that have large lateral dimensions (e.g., bar horns and block horns),
particularly if a nonprimary resonance interferes with the primary resonance. Generally,
the optimum asymmetry is 0. (Also see Uniformity.)
axial resonance -- a resonance where the major amplitudes
are generally parallel to the resonator's axis and there are no nodes on either the input
or output surfaces of the resonator.
axisymmetric -- a cylindrical FEA model whose shape and
material properties do not vary circumferentially around the model (e.g., transducers,
boosters, and many cylindrical resonators). Variations in FEA amplitudes and stresses
occur only in the axial and radial directions; circumferential variations are not
permitted.
flexure -- a vibration mode in which the stack vibrates
transverse to its axis, similar to a bending beam.
horn (probe, sonotrode) -- a resonant device that
transmits ultrasonic energy to a load.
loss -- power dissipated by the stack when running in air.
High loss may indicate a potential reliability problem (e.g., fatigue, galling, transducer
failure, flexure, etc.).
nonaxial resonance -- any resonance other than the axial
resonance.
primary resonance -- the resonance that has the desired
vibration mode. This is often an axial resonance but can also be flexural, radial,
torsional, etc.
nonprimary resonance -- any resonance that is not the
primary resonance.
stack -- an assembly of resonators. The usual plastic
welding stack consists of a transducer (converter), booster, and horn. The usual medical
transducer consists of a transducer and probe.
transducer (converter) -- a resonant device that converts
high frequency electrical energy into high frequency mechanical vibration. The material
that performs the conversion may be either piezoelectric or magnetostrictive.
uniformity -- roughly, a ratio of
two amplitudes on a specified resonator surface (usually the resonator face) that
describes the degree to which the axial amplitude is the same over the specified surface.
Uniformity is denoted by U. Generally, the optimum uniformity is 1.0 (i.e., 100%). (See Asymmetry.)
unshaped resonator -- a resonator whose sides are
essentially parallel to the stud axis. Unshaped resonators appear to have no gain.